The humans behind industrial automation

Automation and other AI-enabled technologies are revolutionizing how we live, work and everything in between.
Smart innovations in engineering and other sectors are superseding yesterday’s jobs and spawning a new breed of tech-savvy employees. Behind every automated system, there are humans at work helping to make our world smarter.
Here are a few of the many people working to automate heavy industry sectors, without whom AI systems couldn’t operate.
System Engineer
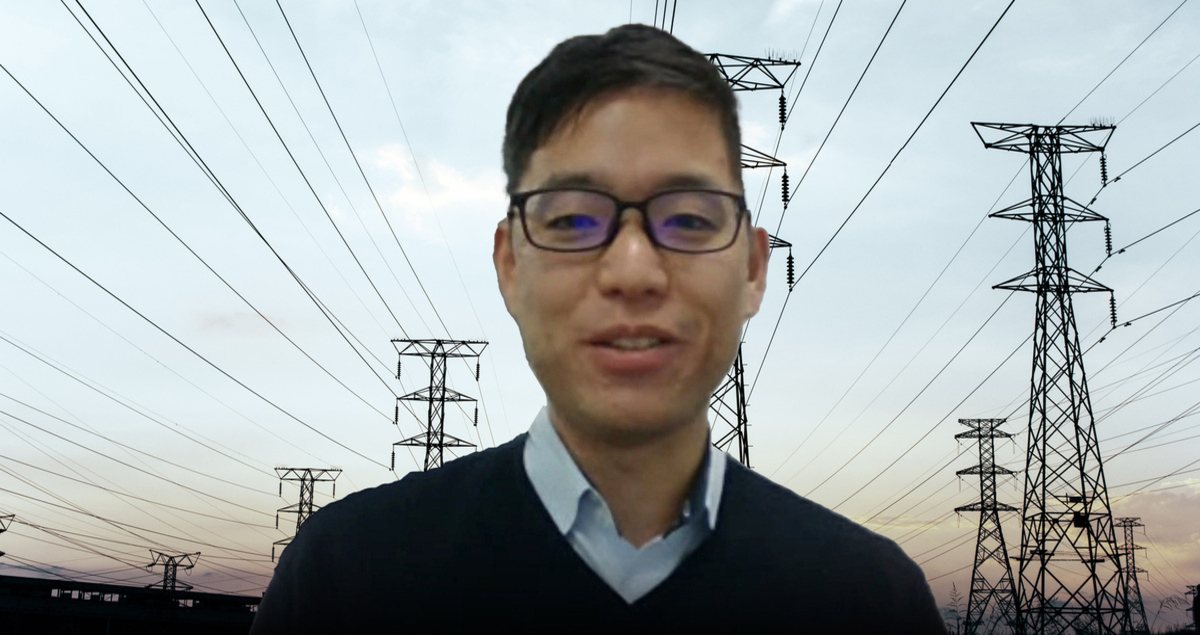
While power plants share a common goal of decarbonizing their operations, each plant is different and has its unique challenges.
That’s why Leandro Hideo Iha and team are developing digital platforms like TOMONI, the suite of intelligent solutions from Mitsubishi Power, a power solutions brand of Mitsubishi Heavy Industries (MHI). They leverage advanced controls, AI and machine learning to make energy systems smarter and more profitable.
“Power plants get old and need to be tuned up over time. Developing automation and machine learning software can help optimize plants without having to solely rely on manual work,” Iha says.
The automated power plant operations are monitored and controlled remotely from any of four TOMONI HUB monitoring centres located across the globe. The platform makes power plant operations safer, more efficient and more sustainable.
“In countries like Japan with a declining population, automated systems can help humans and machines work together to ensure we have the knowledge and manpower to run efficient and reliable power plants,” Iha adds.
Systems Engineer
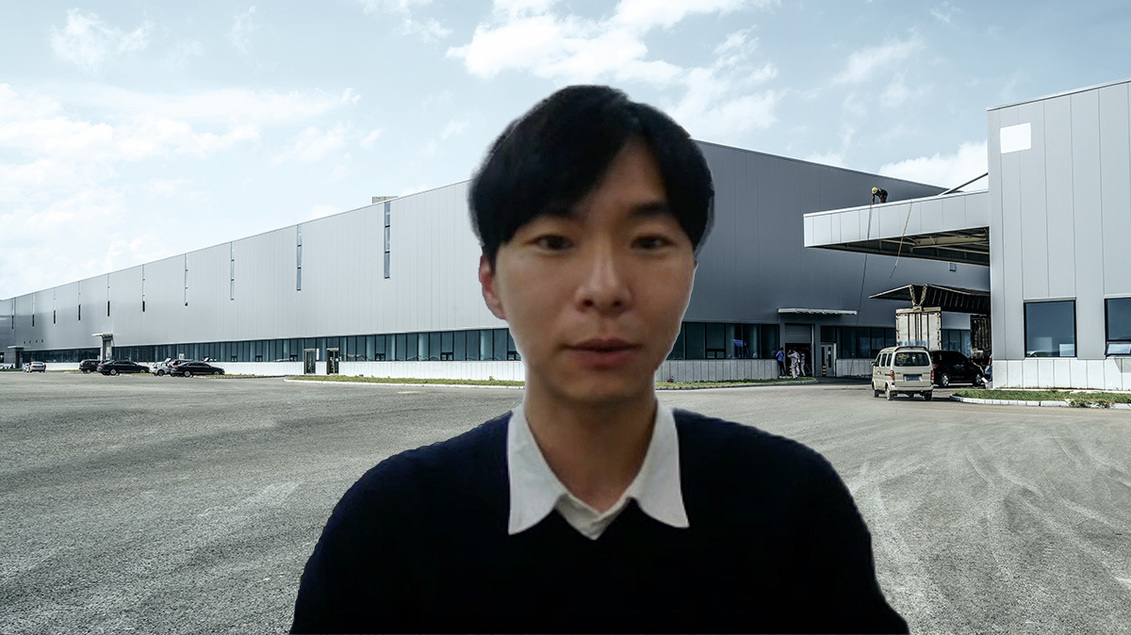
Automated guided forklifts (AGF) are transforming modern warehouse facilities, making operations safer, more efficient and reducing costs.
Shota Tanaka is a systems engineer from Mitsubishi Logisnext, who is working as part of a digital innovation team, designing new features to develop Mitsubishi Heavy Industry (MHI) Group’s AGF-X automated forklift system that picks and processes warehouse orders.
Robot-efficient systems like this are algorithmically designed to avoid collisions and provide a stable lifting environment. These features make warehouse environments safer and enable automated pickers to reach hard-to-access places.
Automated forklifts increase order-picking accuracy and speed, reduce vehicle waiting times, overcome a shortage of operators needed for manual forklift operations and reduce the burden of heavy manual labor.
“Looking to the future, I see the role of automation when developing AGF systems will increase, which will make warehouse operations more efficient,” Tanaka says.
“Automated solutions can calculate rapidly and accurately. But humans need to decide what automation systems calculate and how.”
Product Lifecycle Manager
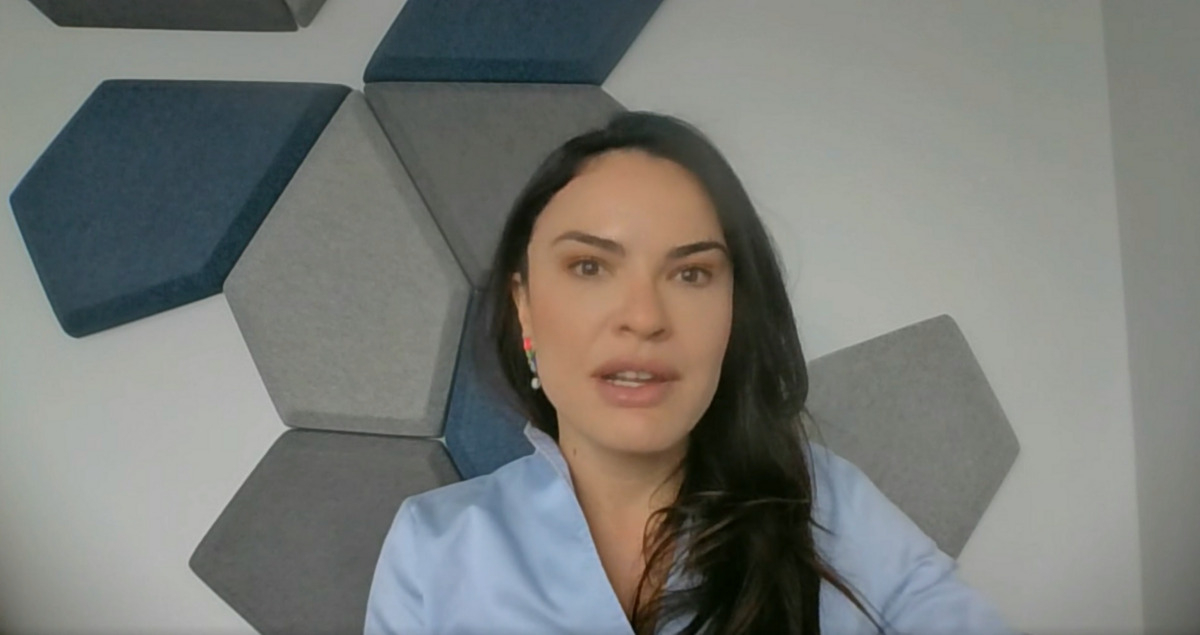
Global steel demand has risen sharply in recent years due to an expanding population and economic growth, leading to an increase in the industry’s CO₂ emissions, according to the International Energy Agency.
As the sector tries to balance meeting global demand for steel and the need to make steel production more sustainable, plant owners are seeking smart solutions to help decarbonize operations.
Hayane Araujo Bragança, Product Lifecycle Manager with MHI Group company, Primetals Technologies, in Austria, has helped develop a software solution called Through-Process Quality Control (TPQC). She works with steel plant owners to understand their challenges and determine how the TPQC platform can meet quality standards and streamline processes to enhance efficiency and sustainability.
“When you think of the steel industry, green steel is the future. But the first step is to optimize and do more with less. When you have the right data analysis and analytics in place, you can reduce waste, you can reduce inefficiencies, and you can reduce energy consumption,” Bragança says.
The platform uses automation to connect and visualize multiple data points from different production steps, but human input behind the scenes is essential, she adds.
“The human factor is at the core of technologies like AI and automation. We still need the right people, in the right places and with the right knowledge to potentialize the benefits of these technologies.”
Digital Innovation Engineer
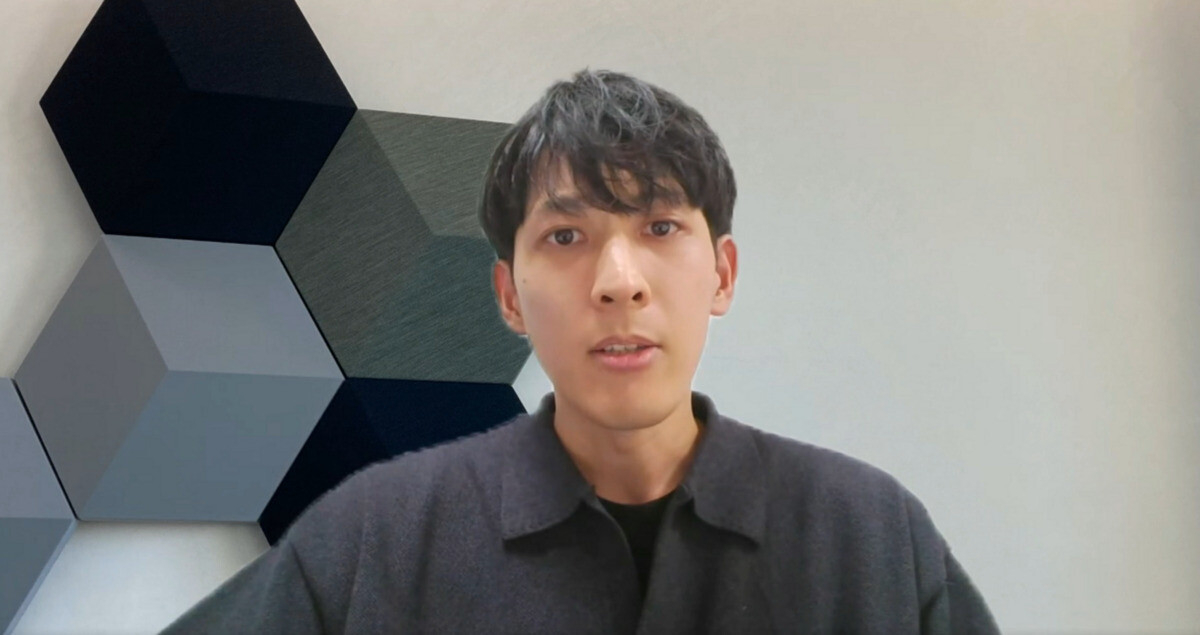
“In addition to machine learning, intuitive algorithms are also a type of AI. Without a large amount of training data, we can empirically get answers close to the correct answer in a short time.” Daishi Irie explains.
As an engineer at MHI’s digital innovation headquarters, he develops applications to make products more intelligent and improve business processes using optimization technology developed in operations research.
The algorithms he helps build combine knowledge and technology to connect humans and machines and promote collaboration, aiming to help solve some of society's key challenges.
His role includes exploring new ways for the company’s ΣSynX (sigma syncs) automation solution to connect machine systems and optimize performance. Applications for the digital platform include facilitating automated order-picking solutions in warehousing systems, like those being developed by Mitsubishi Logisnext.
“Although ΣSynX supports automated operations, humans have an important role to play. Humans design the automation solutions, support the day-to-day operations and help maintain the system,” Irie says.
Related tags
