Testing turbochargers to boost durability and reliability

Every manufacturer seeks to squeeze more out of its machinery: more efficiency, more power, more reliability. This is especially true for engine manufacturers, where “more” is a mandate for their customers in the automotive, aviation, and heavy machinery sectors, among others.
Today’s advanced turbochargers help meet these demands. In fact, we’re in the early stages of what’s shaping up to be the “Golden Age of Turbochargers.” The technology may still conjure images of high-performance cars, but increasingly, turbochargers are common in ships, trains, buses, and even construction machinery and generators.
First used in the 1920s, turbochargers increase engine horsepower by tapping into the energy that the engine’s own exhaust gases produce. What should go out, goes back in and delivers extra thrust.
This power and efficiency boost is valuable to automakers like General Motors, Volkswagen, Honda, and BMW, all with plans to increase their vehicle fuel economy by 3.7 percent year-over-year between 2022 and 2026.
At the end of this period, the turbocharger market will stand at nearly double what it was in 2018, amounting to $32.4 billion, with more than 20 percent of vehicles running on turbocharged power.
This will include electric vehicles, which are expected to play a pivotal role in decarbonizing transportation. Vehicles with electric powertrains will benefit from turbochargers extending the distances they can travel between charges, addressing a key consumer concern.
Turbochargers that keep going … and going
Future advances in reliability and performance will depend on sophisticated approaches, like those in use at Mitsubishi Turbocharger, a part of Mitsubishi Heavy Industries (MHI) Group and a top manufacturer of high-quality turbochargers.
At MHI’s testing facilities in Sagamihara and Nagasaki, Japan, 100 different tests on turbocharger components are performed. The following five tests illustrate the state-of-the-art technology and painstaking work needed to ascertain the reliability, functionality and safety of turbocharged engines prior to production.
They tell the evolving story of endurance in modern manufacturing.
Test 1: Drive shaft motion
Extending a turbocharger’s lifespan begins with setting ambitious goals. For Mitsubishi Turbocharger, the aim is a unit that lasts a minimum of 150,000 driving miles, with an optimum target of double this figure. To increase durability, researchers must find ways to reduce the stress on the turbocharger shaft.
MHI conducts a motion test on a turbocharger’s components, which is a critical part of its noise, vibration, and harshness performance. A typical turbocharger has two wheels connected to a common shaft. When in motion, the shaft undergoes vibration and stress that can cause a breakage.
Sophisticated acoustic testing technology is used to balance vibrations evenly across the shaft. “It’s all about the frequency,” says Frank Flores, assistant manager at Mitsubishi Turbocharger and one of the company’s “masters of reliability”. The shaft is “either well-balanced or it’s unbalanced.”
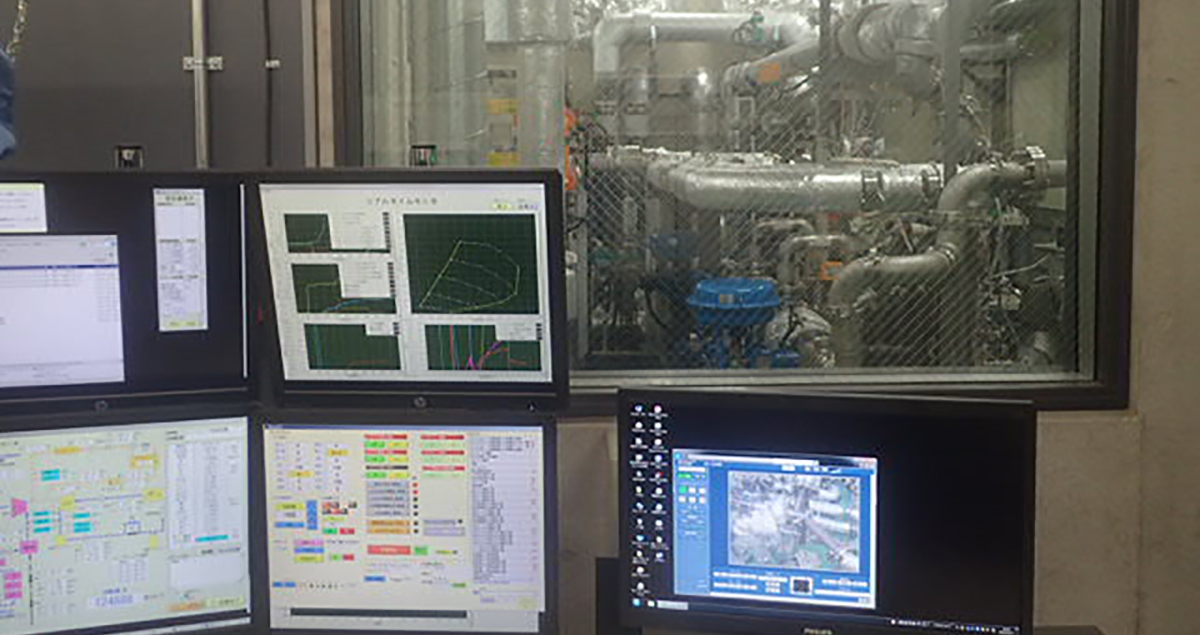
Test 2: Thermo cycling reliability
In manufacturing, it’s important to understand the biggest threats to equipment before you can combat them. For instance, every turbocharger suffers from severe temperature fluctuations that affect long-term productive use and lifespan. The turbine housing, the structure that holds together a turbocharger’s components, is particularly vulnerable to these thermodynamic stressors. Different materials — different grades of steel, iron or aluminum, for example — react differently to temperature fluctuations.
MHI engineers test turbine housing materials under extreme conditions to text how well they maintain their structure. “The target is to see if the material can withstand this cycle and won’t crack, warp, or deform,” Flores says.
In one example of multi-cycle testing, the team opens an engine’s throttle to maximum revs for about two minutes, and then lets it fall back to idle for 30 seconds. The process of cycling up, and cycling down, is repeated for as many as 200 hours to evaluate which materials copes best.
Test 3: Thrust bearing endurance
All turbochargers contain highly engineered precision bearings that enable the machinery to operate at high speeds. Excessive heat or friction pose a threat.
Thrust bearings are static bearings allowing rotation between a turbocharger’s parts. Different temperature cycles generate different levels of friction, which can interfere with the bearings and compromise performance. To combat this, the bearings are lubricated with motor oil. But each turbocharger is different, requiring a specific volume and oil thickness to maximize performance at different temperature cycles.
To minimize friction, engineers test various types, volumes and thicknesses of lubricants and oil additives. The challenge is to adapt these tests to the specific thrust-bearing specifications that an original equipment manufacturer provides. In each case, researchers test different oil compositions to find a solution that optimizes high-speed efficiency.
Test 4: Moment of inertia
Vehicle inertia describes how mass is distributed across a vehicle, which affects performance. Rear-engine vehicles, for instance, perform differently to front-engine vehicles, partly because the center of mass is different.
An engine performs most efficiently when its total mass is evenly distributed around its center of mass. This principle also applies to the wheels inside a turbocharger, such as the compressor wheel and the exhaust gas turbine wheel. They perform best given even distribution.
MHI tests various wheels made of different materials, like titanium aluminide or Inconel (a heat-resistant nickel-chromium-based superalloy), to determine which materials rotate best by completing the most revolutions in a specific time period.
Test 5: Turbine wheel burst containment
As frightening as it sounds, centrifugal forces can shatter the housing of wheels inside a turbocharger. If they do, wheel components can penetrate the interior of the vehicle itself and injure the driver or passengers.
To prevent this happening, MHI tests the integrity and reliability of both housing and wheels, particularly those in new-generation, high-performance turbochargers, designed to outperform previous designs.
Researchers simulate scenarios where wheels shatter from stress, overspeed, and other factors, to verify the housing is sturdy enough to contain flying debris. They put different housing materials under extreme conditions to stress-test the containment, ensuring passengers stay safe.
These five test methodologies represent just the tip of the iceberg. As Flores notes, the teams in various testing facilities — Sagamihara, Nagasaki, the Netherlands — are always striving for frictionless perfection in testing turbocharger reliability, durability, and functionality. In that way, they give original equipment manufacturers more of what they’re looking for and, in so doing, pass the ultimate test.
Related tags
