Net zero aviation: the multiple pathways to decarbonization

This article was previously published in our newsletter, if you're not already a subscriber, sign up here.
Since I was a child, the smell of unburned hydrocarbons from jet aircraft on the tarmac sent a chill down my spine with the feeling that something exciting and powerful was going to happen. In the light of the climate grand challenge, this smell also signals emissions since every kilogram of kerosene produces 3 kg of carbon dioxide. In cruise, an airliner burns about 1 kg per second so one hour of flight yields about 10 tons of CO₂. Adding up all flights and operations, roughly 2.5% of global CO₂ emissions come from the aviation sector.
Aircraft engines also produce nitrogen oxides, soot and water vapor. At altitude these can create contrails which increase radiative forcing. It is clear that aviation’s effect on the climate is significant and seriously in need of abatement.
Industry is already working hard to decarbonize and so are its suppliers, while regulators and governments are putting both rules and incentives into place. The challenge is that meeting the 2050 net zero target that IATA, the airline trade body, has set itself is extremely challenging in a sector with decade-long lead times. It will require multiple pathways and technologies, unprecedented collaboration and an ‘all of the above’ approach.
A multi-pronged approach
The lowest-hanging fruits are operational measures that are quick and offer rapid paybacks, such as imposing stricter weight limits on flights, adding more seats into cabins and incentivizing pilots to fly and taxi more efficiently. Making better use of available air space – such as the Single European Sky program and NextGen in the US – will also help. The impact of improvements in air traffic control is maybe a 6-12% reduction in emissions over 20 years.
Upgrading aircraft engines has a greater decarbonization potential, say 15-20% savings in fuel burn, depending on the current state of an airline’s fleet and how rapidly it is replaced. Many airlines have started to wash their jet engines since removing even tiny residue from engine parts improves fuel efficiency. Modern aircraft like the A350, B787 and B777X use composite materials and advanced aerodynamics to reduce weight and drag, reducing fuel burn and thus emissions.
An important area currently being explored are electric, turbo-electric or hybrid electric propulsion systems. Independent of whether the energy carrier will be batteries, sustainable aviation fuel (SAF), hydrogen, or ammonia each of them will require an electrical machine to convert electrical work into mechanical work which can then be used to propel the vehicle.
New tech, new challenges
For batteries, it is the lack of energy density, as a quick look at the numbers demonstrates. Kerosene has an energy density of 12,000 watt-hours per kilogram. Since the best gas turbine aero-engines are around 50% efficient, the useable work output is about 6,000 Wh/kg.
The average battery energy density today is around 150 Wh/kg and this may reach 600 Wh/kg a decade from now using advanced battery chemistries. Compared to hydrocarbon fuel, this is one order of magnitude lower, which is why battery electric systems will likely be restricted to small airplanes and for urban mobility.
Hydrogen-based aircraft are being worked on by both large manufacturers, including Airbus, and start-ups like Universal Hydrogen. A key challenge here is low volumetric fuel density. Depending on the aircraft mission, the tanks for gaseous hydrogen would have to be very large and thus heavy.
Liquifying the hydrogen so it is denser mostly overcomes the first problem but creates a second, since cryogenic hydrogen (stored at -250˚C) boils off at a significant rate of 48% a day. There are however other ideas being explored. Advanced engine cycles could take advantage of the cryogenic properties of hydrogen, for example using it as a heat sink or collecting the produced water and injecting it as steam to increase thrust and to mitigate contrails and NOx emissions.
Another energy carrier option to reducing CO₂ output is SAF. One advantage is that it can use current infrastructure and already over 400,000 flights have taken off where some SAF has been blended into the fuel mix. And in a welcome sign of collaboration, the big energy majors are investing alongside their customer airlines to scale production. However, there are not enough inputs currently, whether that is waste oil for biofuel or renewable power to generate electro fuels such as e-SAF or e-methane, and the costs are currently uneconomic.
A different approach to cutting emissions could be by reducing demand. This May, France banned short-haul flights where the same trip can be taken by train in 2.5 hours or less. But scaling this approach to intercontinental flying is not a real option due to a current lack of alternate emission-free transportation. Also, it could have a catastrophic impact on the global economy and could endanger lives by disrupting supply chains for critical goods like medicines.
MIT & MHI
Meanwhile, the MIT Gas Turbine Laboratory (GTL) and Mitsubishi Heavy Industries (MHI), among many others, are working hard on tackling these challenges. Through our long-standing strategic collaboration with MHI, we are currently creating a high-power density megawatt (MW) scale electrical machine to help transform aviation and other transportation sectors. Our 1MW motor demonstrator is a key stepping stone to electrifying larger aircraft. We have a great team of experts with vast experience in each of the critical areas. This makes the whole greater than the sum of the parts.
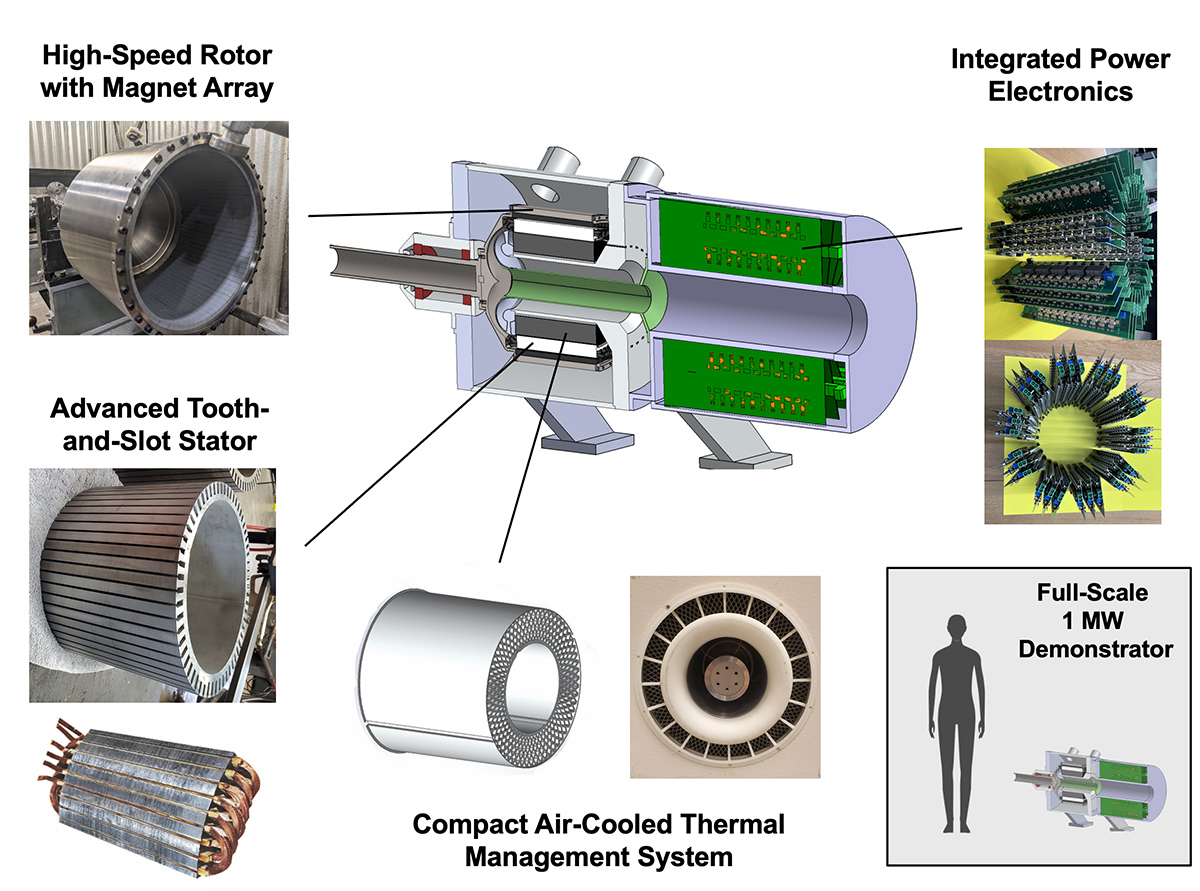
The project is an industry strength program where major emphasis is put on risk mitigation. This is done with hardware mock-ups of key components using rapid prototyping, manufacturing and assembly demonstrations of critical parts, and component rig test experiments to characterize performance. It has been a true privilege collaborating with MHI and an invaluable experience for the students to see the ideas turned into hardware and potentially future products.
Discover more about MHI's aircraft business
Related tags
