Metallurgy magic: How to forge a path to green steel

This article was previously published in our newsletter, if you're not already a subscriber, sign up here.
It is a stark but unavoidable fact that producing a ton of steel today produces almost two tons of carbon dioxide emissions. And since steel is such a vital part of our infrastructure – from buildings to cars to wind turbines – the iron & steel industry as a whole is responsible for a significant slice of global CO₂ emissions: some 7-10%.
Making steel sustainable, by using new technologies, cleaner energy sources and optimizing the production process, is therefore a critical step in tackling climate change. As a leading equipment and technology supplier to the global metals industry, I believe Primetals Technologies, a Mitsubishi Heavy Industries (MHI) Group company, can play an important role in helping the world’s steelmakers forge a path to green steel.
As steel is a huge industry, there are many suppliers, of course. But most only cover a part of the product portfolio. There are only three that supply equipment and technologies globally and across the steelmaking lifecycle: from the upstream iron ore beneficiation and pelletizing and supply of scrap to the meltshop with its furnaces, converters, electric arc furnaces and casters, to downstream plate, strip and long rolling mills.
At a time when operators are increasingly demanding end-to-end solutions that incorporate the know-how to achieve carbon neutrality, project size is increasing and so is the market share of the top three players.
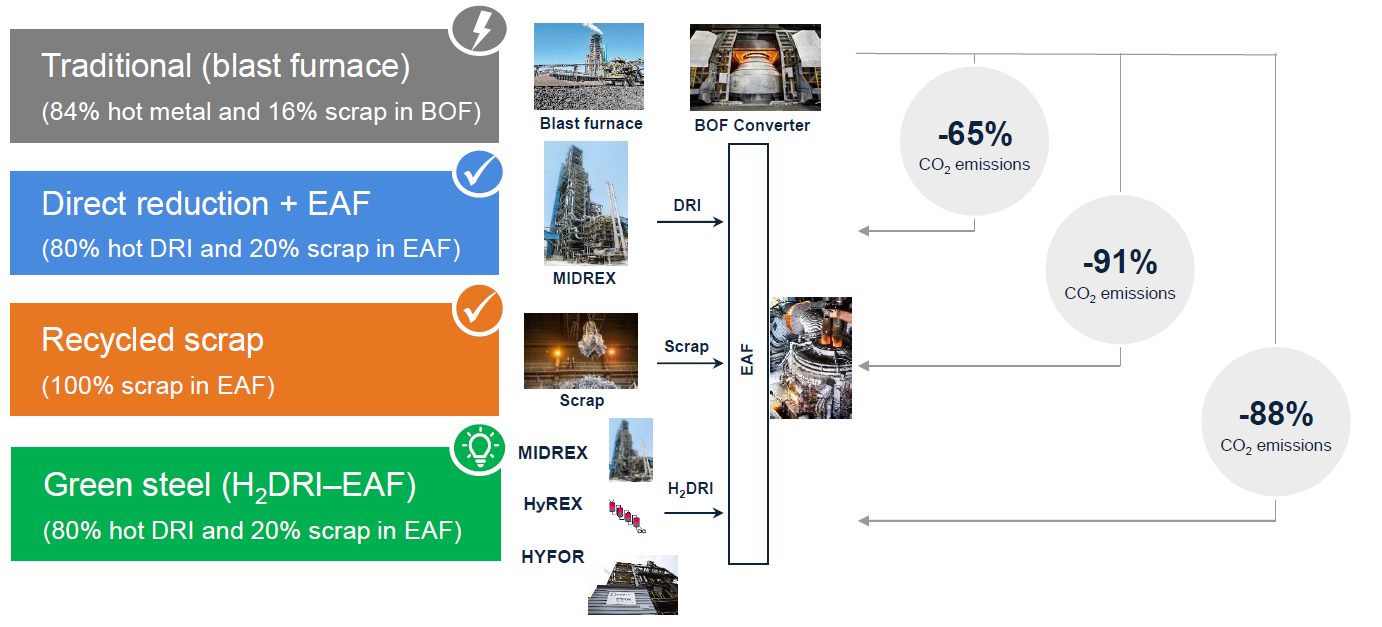
From optimization to innovation
The first step for steelmakers is to optimize current production. Fortunately, existing technologies can relatively easily achieve CO₂ reductions of up to 40% by, for example, various innovative gas injection technologies for blowing oxygen and hydrogen into a traditional blast furnace; by replacing some iron ore-based hot metal with steel scrap; and by using advanced automation tools like digital twins or Through Process Optimization for real time monitoring of the plant and avoiding unplanned downtime as well as assuring quality aspects of the final steel product. These measures can also reduce the amount of by-products and cut emissions from the stack, as well as increasing yields and reducing costs.
It gets even more interesting once an operator is ready to switch to new technologies – and with some 70% of today’s blast furnaces needing relining or to be replaced by 2030 as they come to the end of their life, there is an opportunity to take advantage of two innovations: electric steelmaking and the direct reduction of iron ore (DRI).
Using an electric arc furnace and feeding it entirely with scrap can eliminate over 90% of CO₂ emissions and many operators are installing and testing these, initially mostly to run alongside existing furnaces in the meltshop. However, there is not enough scrap and certainly not enough high-quality scrap available to make this an industry-wide solution.
This is where DRI (removing oxygen from iron ore without melting it) can play a vital role. It allows an immediate cut in CO₂ emissions and instead of sintered iron ore, it produces so-called hot-briquetted iron (HBI), which is easily transported and can be used in both a blast furnace and an electric arc furnace. The MIDREX direct reduction process, for which Primetals Technologies is a licensee, can help reduce emissions by two-thirds with a mixture of 80% HBI and 20% scrap in an electric arc furnace – though, again, there are supply constraints, in this case the lack of high-quality iron ore.

Going completely green
To achieve fully green steel by eliminating carbon emissions entirely requires further steps and investment depending on the production process. Operators using DRI have to switch from natural gas to 100% low-carbon hydrogen for their reducing agent, for example by using our own HYFOR technology and HyREX, a joint development with POSCO in South Korea. We are trialing both innovations, HyREX with POSCO and HYFOR with voestalpine in Austria.
And while those using electrification have effectively erased emissions from the steelmaking process itself, they have to ensure that the electricity powering their electric arc furnaces is zero carbon too. Given the amount of electricity required for a growing number of such furnaces, especially in the context of continued increases in global steel demand, this will require a rapid expansion of the renewables sector – which, in turn, will consume more steel!
Potentially, next-generation nuclear reactors could also provide carbon-free power for electric arc furnaces. Whether this is politically feasible will vary from country to country, though attitudes to nuclear energy have grown markedly more positive over the past couple of years.
For operators that need to sequence their transition, carbon capture and utilization technologies can reduce emissions in the meantime, for example MHI’s KM CDR process and LanzaTech’s microbe-based gas fermentation. There are also secondary treatments that can help reduce both waste and energy intensity, such as Primetals Technologies’ Arvedi ESP (endless strip production) process, or using vacuum applications to eliminate impurities from liquid steel.
By continuing to invest in our own technological development, we are confident that Primetals Technologies can help one of the world’s key industries to decarbonize. Steel is by nature sustainable: it has a myriad uses and can be recycled almost forever. This makes it an ideal raw material for the circular economy of the future that we all want to achieve.
Discover more about Primetals Technologies' lectures on green steel
Related tags
