Let a robo-suit do the heavy lifting for you

The word 'exoskeleton' conjures up images from movies like Ironman or Alien.
But exoskeletons are no longer just science fiction. They are being developed for a wide range of markets, including medicine, manufacturing and construction.
Exoskeletons help disabled people walk again, take on heavy lifting in industrial settings and even assist in the clean-up of nuclear accidents.
With such a wide range of applications, it is unsurprising that the market for exoskeletons is predicted to grow to US$2.1bn by 2021.
Learning to walk
The idea of exoskeletons is nothing new.
A US patent was awarded in 1890 to Russian inventor Nicholas Yagn for an “apparatus for facilitating walking, running and jumping.”
Just like Yagn’s early prototype, the overwhelming majority of exoskeleton designs have focused on assisting movement, largely for those who have lost it due to disease or injury.
These can be used to either assist mobility during rehabilitation, or to provide an alternative to a wheelchair.
The Ekso GT from Ekso Bionics is an example of the former, designed to help patients who have suffered strokes or spinal cord injuries get back on their feet sooner. It supports the re-learning of step patterns and weight shifting, literally enabling the patient to learn how to walk again.
Likewise, the REX supports rehabilitation, but it also enables patients to use it as an alternative a wheelchair: unlike many other exoskeletons on the market which require the patient to use crutches, the REX is capable of completely supporting a patient’s weight, truly giving them robotic legs.
Offloading industrial workers
Industrial applications are another area where exoskeletons are starting to come into their own.
Despite increasing levels of robotics being used in factories, manufacturing, warehousing and construction often still require humans on the shop floor to lift weighty items, often for prolonged periods of time.
Handling heavy materials and the supporting tools are contributors to fatigue and musculoskeletal disorders, which account for around 30% of lost time workplace injuries and illnesses in the US alone.
US insurance company Liberty Mutual in 2014 estimated the direct costs of injuries due to overexertion from activities such as lifting, pushing and pulling to be US$15.1 billion – representing one quarter of total US workplace direct injury costs.
For many employers, it therefore makes economic sense to invest in technology that can avoid in such injuries.
There are now a vast variety of exoskeleton products available for industrial applications – both passive mechanical systems that simply transfer the weight from one part of the body to another, and power-assisted technologies.
Ekso Bionics has expanded the use of its suit into the construction arena. The Fortis exoskeleton from Lockheed Martin enables factory workers to hold heavy hand tools to reduce muscle fatigue.
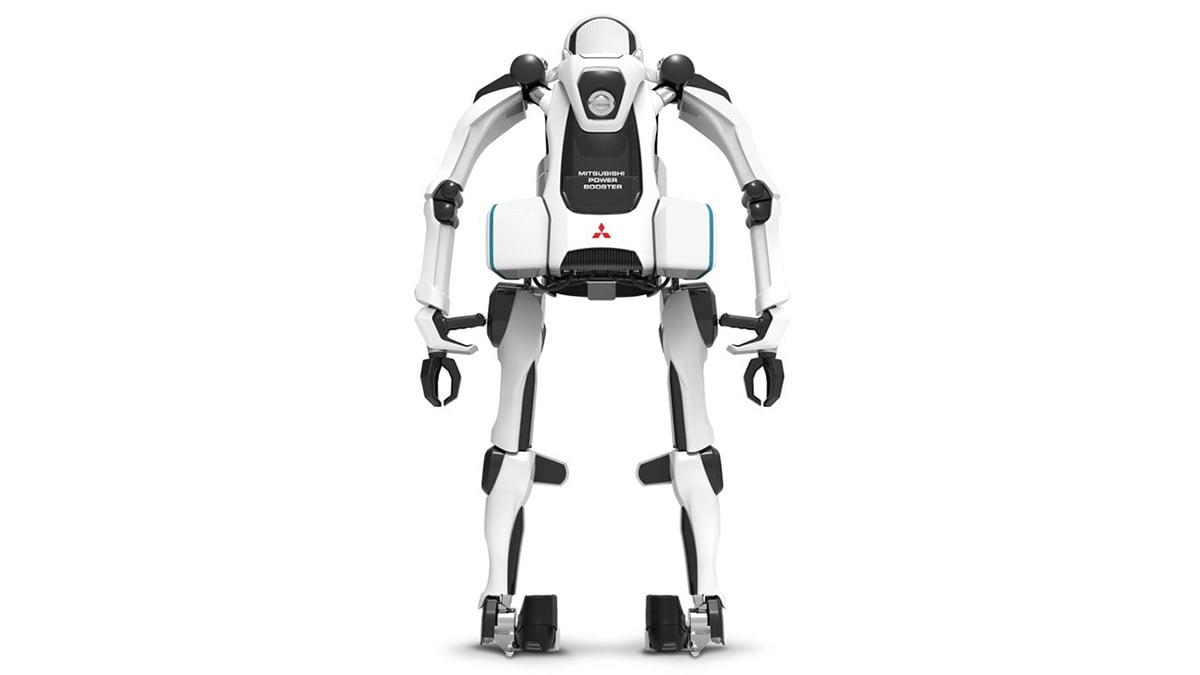
Picking the right arms and legs
Key to designing an effective exoskeleton is providing human users with power that exceeds their own - without impeding the wearer’s ability to move naturally. One example of how far Exoskeletons have advanced is Mitsubishi Heavy Industries Group’s Power Assist Suit (PAS).
Originally developed jointly with the Japan Atomic Power Company to be able to work in a radiation-contaminated environment (e.g. nuclear accidents), PAS can assist with heavy work in a range of settings.
Wearing the PAS, a worker can handle approximately 40 kilograms (kg) of extra weight.
PAS is powered by a compact, lightweight unit comprising a lithium-ion battery and small-scale high-output motors typically used in robots for nuclear applications, plus small-scale circuit boards. PAS is anchored to its wearer only at the hips and feet, and is controlled by foot movement via sensors attached to the soles of the worker’s boots.
Using predictive analytics algorithms on sensor data from the boots, PAS can even learn a person’s step pattern to match their natural walking speed.
The upper and lower robotic limbs which make up the suit are modular, so can be selected to meet the needs of individual industrial applications.
MHI is now working on enhancing the PAS concept. These range from construction and civil engineering, to work in assembly plants and transporting injured people after an accident.
So, while we may not have an Ironman suit in our wardrobe anytime soon, exoskeletons are set to make their mark in an ever-wider range of applications in industry and elsewhere.
Related tags
