It’s a breeze: How a small island started making the world's biggest wind turbines

If you were asked to picture the center of the world's offshore wind turbine industry you might think of somewhere in China or perhaps Germany's industrial heartland.
You almost certainly wouldn't picture a small island off the south coast of England most famous as a holiday destination.
In fact, the Isle of Wight has a long and distinguished history when it comes to the development of world-leading technology -- from shipbuilding to the aerospace industry.
Today, a factory on the island makes the largest serially-produced turbine blades in the world, and is at the heart of a thriving and highly-skilled engineering hub.
Island of innovation
When the White family moved its shipyard to the Isle of Wight in the early 19th century, a long and unusual history of engineering began.
Starting with shipbuilding, the island became home to Saunders Roe, which specialized in "flying boat" sea planes and went on to win the contract to build the world's first hovercraft.
The expertise honed through these industries later built Westland Helicopters and even space technology projects like the Black Knight Rockets.
The composite technologies developed by the ship and later the aircraft industries meant the skills on the island were ideal for manufacturing turbine blades -- which are, in many ways, like an aircraft wing.
Both require the highly specialized process of lamination -- applying multiple layers of composite, such as fibers, resin and a catalyst, to produce a material which is unusually light and incredibly strong.
The skills that the island's engineers developed making immensely sturdy and durable aircraft wings are now being used to make turbine blades with exactly the same qualities.
The wind turbine industry on the island has seen plenty of changes over the last 20 years as Aero Laminates became NEG Micon, then Vestas and finally the joint venture that exists today, MHI Vestas Offshore Wind.
The company has two manufacturing sites on the island. In 2017, it also repurposed a decommissioned oil-fired power plant on the mainland in nearby Southampton, turning it into a state-of-the-art finishing, and logistics facility. A giant barge takes wind turbine blades from the island across the water to be painted there.
The MHI Vestas sites have brought valuable skilled employment to an area which, like many other coastal communities in the UK and elsewhere in the world, is relatively economically deprived.
Just as the island's rich history of innovation benefits the wind turbine industry, the industry is making a major contribution to the region's socio-economic development.
Record-beating blades
The boom in wind power investment, driven in part by the need to mitigate the effects of climate change, has meant rapid growth in the sector and huge strides in the capabilities of individual turbines.
The V164 9.5 MW offshore wind turbine stands at 195 meters from sea to blade tip -- twice as high as the Statue of Liberty. Each blade is bigger than the wingspan of the 747 jumbo jet and a single turn can power an average UK home for 29 hours.
100 of these massive turbines are being installed in the Moray Firth off Scotland's East Coast where they will power around 1 million homes by 2022. Another 90 will be sited at Triton Knoll off England's east coast, generating enough energy for a further 800,000 homes.
The United Kingdom is leading the world in wind power generation, not only by commissioning such large wind farms but also through its exports to Europe and the rest of the world.
The blades for these turbines are manufactured using the latest composite production technology. As turbines have quickly grown from 1.6 MW systems to their current 9.5 MW capability, world class manufacturing and composite technology have grown with them.
Laser measurement and guidance combined with uniquely structured composite materials ensure that the massive strains borne by parts of the turbine are distributed throughout the structure.
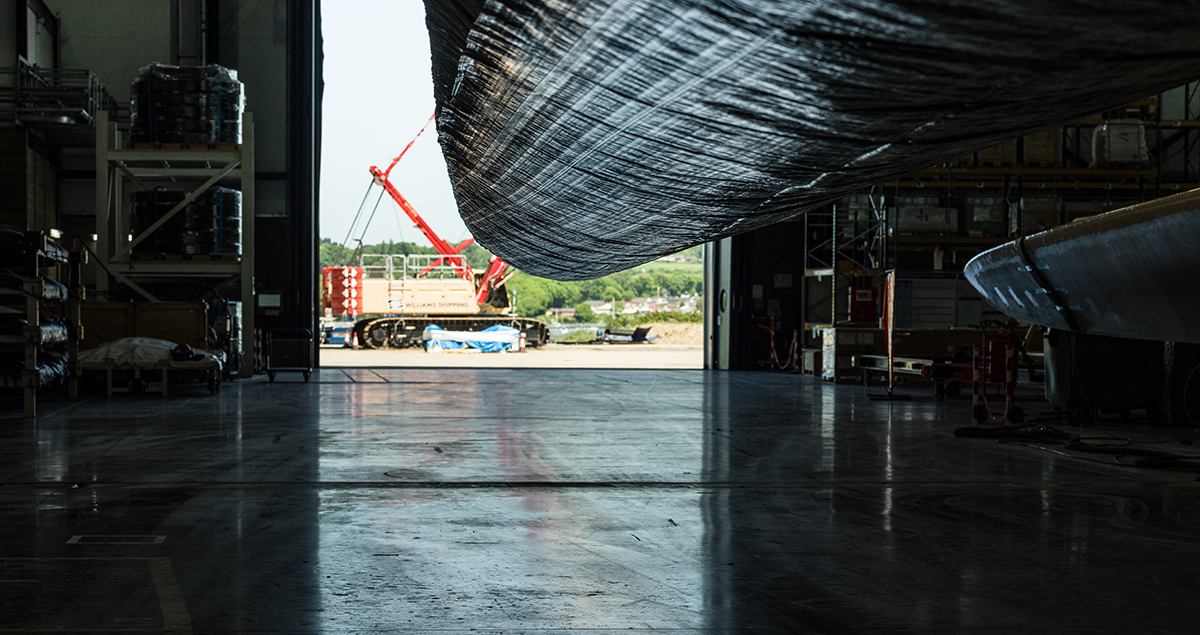
Home-grown talent
The success of MHI Vestas is a success for the region, with the company supporting a wide supply chain, a growing skills base and significant investment in training the local workforce.
The company has invested £1 million ($1.3 million) in training programs and works closely with the recently opened Centre of Excellence for Composites, Advanced Manufacturing and Marine at the Isle of Wight College, which has a workshop modelled on the working environment at MHI Vestas.
There is no better example of how this can benefit the island than James Luter, Director of Production for MHI Vestas Offshore Wind Blades UK Manufacturing.
A local boy who studied at Southampton, James was planning to move away from the island until his mother convinced him to apply for a job at the local blade factory.
Since beginning his wind power career at the company, he hasn't looked back. James is now responsible for all blade production on the Isle of Wight, including more than 300 people who produce the 80m blades for the company's V164 turbine platform.
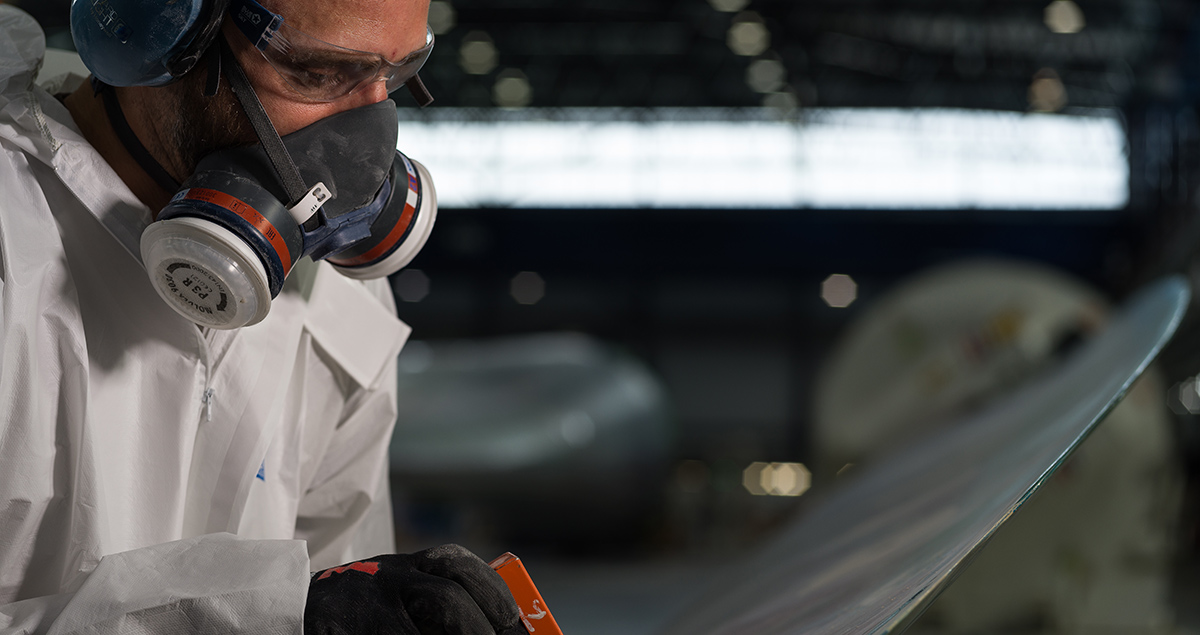
Surging demand
The Isle of Wight is a proud example of the way the wind power revolution is helping communities that have missed out on many of the benefits of globalization.
With the world shifting rapidly to invest in technologies that promote decarbonization, the wind power industry is set for extraordinary growth.
That growth will see innovation hubs in several locations around the world making the next generation of turbine blades, securing highly skilled engineering jobs and revitalizing local communities whether it's in Asia-Pacific or the US.
Related tags
