How IoT smart sensors can make power plants more efficient

The human brain is bombarded with information on a daily basis — the equivalent of 34 gigabytes each day, or enough to overload the average laptop within a week, researchers suggest. Harvesting this volume of data is one thing, but processing and putting it to work is another.
This is where smart sensors come in. Remotely connected sensors — which form the basis of the Internet of Things (IoT) — are all around us, in smart watches, regulated temperature or lighting systems in buildings and, increasingly, in industrial processes and energy infrastructure.
The global smart sensor market is expected to reach almost $78 billion by 2028, more than doubling from almost $32 billion in 2021.
Digital platforms like Mitsubishi Heavy Industries (MHI) Group’s TOMONI suite of intelligent solutions use IoT smart sensors to harvest operations data from power plants. They crunch billions of data points in real time to optimize a plant’s operating efficiency, reduce costs and minimize maintenance and downtime.
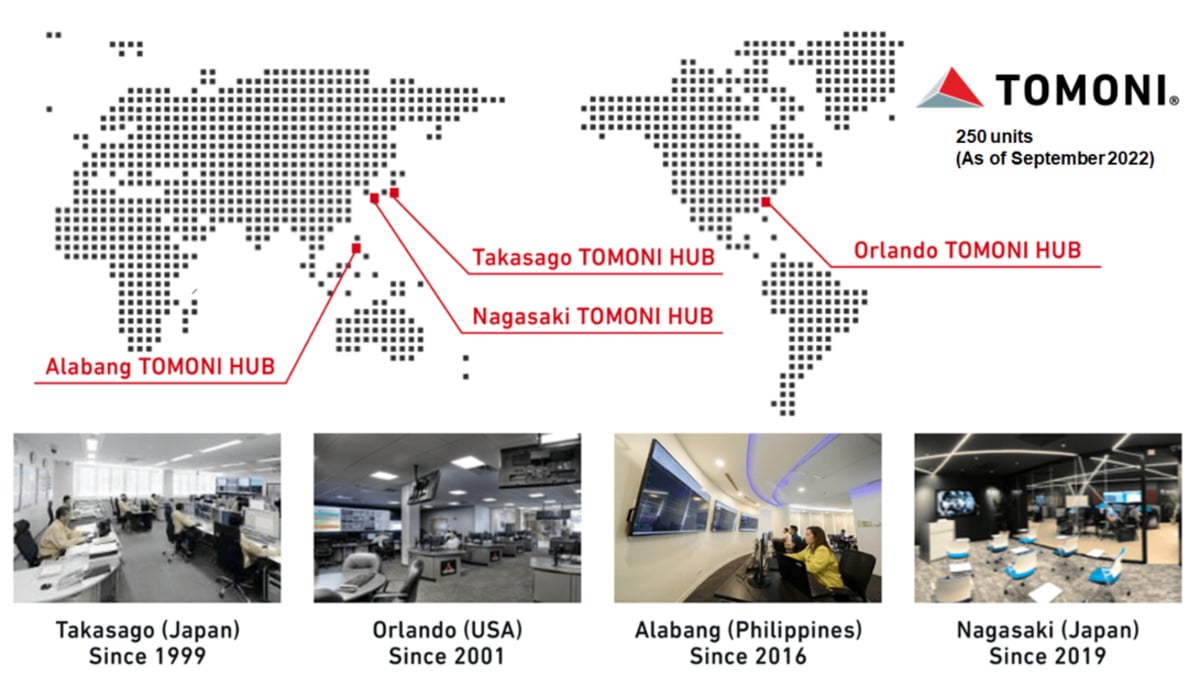
A new breed of ‘soft sensors’
While fully automated power plants are still some way off, platforms such as TOMONI are working to automate many of the individual operations and processes that make a power plant tick.
Once its smart sensors have harvested on-site power plant data, they transmit this information to TOMONI cloud, where powerful machine-learning algorithms process the data to determine optimal operating conditions and maintenance requirements at each power plant.
Remote monitoring is done at one of four regional TOMONI HUBs, located in Takasago and Nagasaki in Japan, Orlando in the US and Alabang in the Philippines.
And fast-evolving technology means these sensors may soon be able to do more. For example, measuring the quality of fuels used at a power plant is costly and time consuming, but a new breed of ‘soft sensors’ is being developed that can predict quality properties from simpler measurements like temperature, pressure and other data in real time.
Data from these soft sensors, combined with traditional sensor data, enables machine-learning models to optimize fuel efficiency at each power plant, meaning they can use less fuel to generate more energy.
Real-time smart maintenance
Smart sensor technology also enables TOMONI HUBs to detect potential problems in power plant operations before they occur.
Identifying maintenance concerns early can avoid costly breakdowns, as engineers can plan and carry out maintenance in advance. This also enables power plant operators to get the maximum working lifespan out of their equipment.
Next-generation sensor technologies used by platforms such as TOMONI have enormous potential to make power generation more fuel efficient and reduce CO₂ emissions.
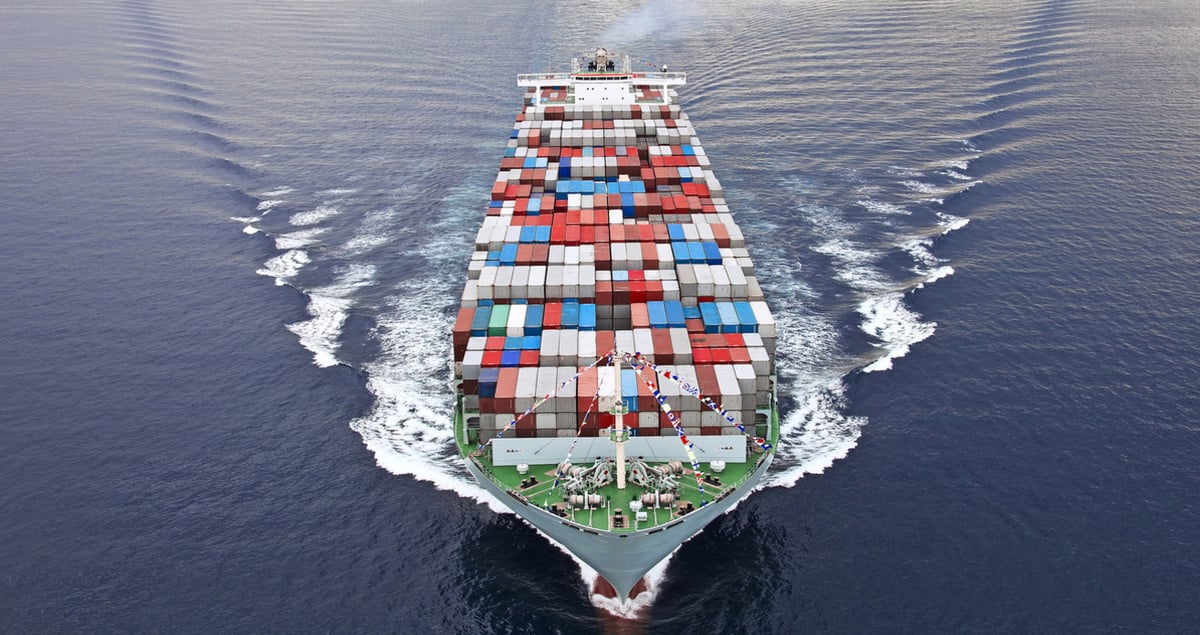
A sensor-loaded world
In a world fueled by data, sensors are here to stay. AI-enabled smart solutions and automation are redefining what’s possible, creating a new world of opportunities in many sectors.
Devices fitted to individual shipping containers as they move around the globe could help make global supply chains more efficient and transparent. Tracking the location of ocean-going cargoes, sea conditions and port arrival times helps streamline logistics.
Tomorrow’s sensors could be powered by vibrations, heat or light, and be stored in devices called supercapacitors. A back-up battery may be needed in case the sensor is starved of power, but it should never need replacing.
Human movement could even power sensors worn on the body, to monitor heart rate, breathing or specific health conditions.
Real-time data harvested by smart sensor connectivity could prove a vital tool to monitor and maintain everything from the human body to energy infrastructure.
And these tiny devices can have a big impact on how power plants operate, enhancing not just efficiency, security and operation costs, but also boosting industry efforts to achieve net zero emissions.
Discover more about Mitsubishi Power's TOMONI suite of intelligent solutions
Related tags
