How hydrogen can help industry escape future natural-gas crises

From steel to fertilizer and beer: a global shortage of natural gas is driving up prices to the point where vital industries are threatened.
This gas crunch is being keenly felt in Europe. In the UK, for example, fertilizer production was halted in September 2021 which, in turn, created a shortage of its by-product CO2 for essential industries such as the food and drink sector.
Shutdowns like the UK fertilizer plants have so far only occurred due to financial constraints – gas prices became too high for production to be profitable. However, they highlight how dependent many industries are on a single fuel and the significant economic disruption any future, genuine natural-gas shortages could bring.
Steelmaking, for example, relies on natural gas not only as a feedstock for primary iron-ore reduction but also indirectly, as a heavy user of electricity for electric arc furnaces, which recycle scrap metal.
Elsewhere, natural gas-fired power plants provide vital backup when renewable electricity isn’t available. Their importance was again highlighted in the UK in September 2021 when they provided much of the country’s electricity during a prolonged period of low electricity generation from offshore wind.
These industries must find a way to protect future production and ensure secure supply of the energy sources they need to operate. They must do so while also recognizing the need to decarbonize and prepare for a net zero future. The answer to both could lie in carbon-free, ‘green’ hydrogen.
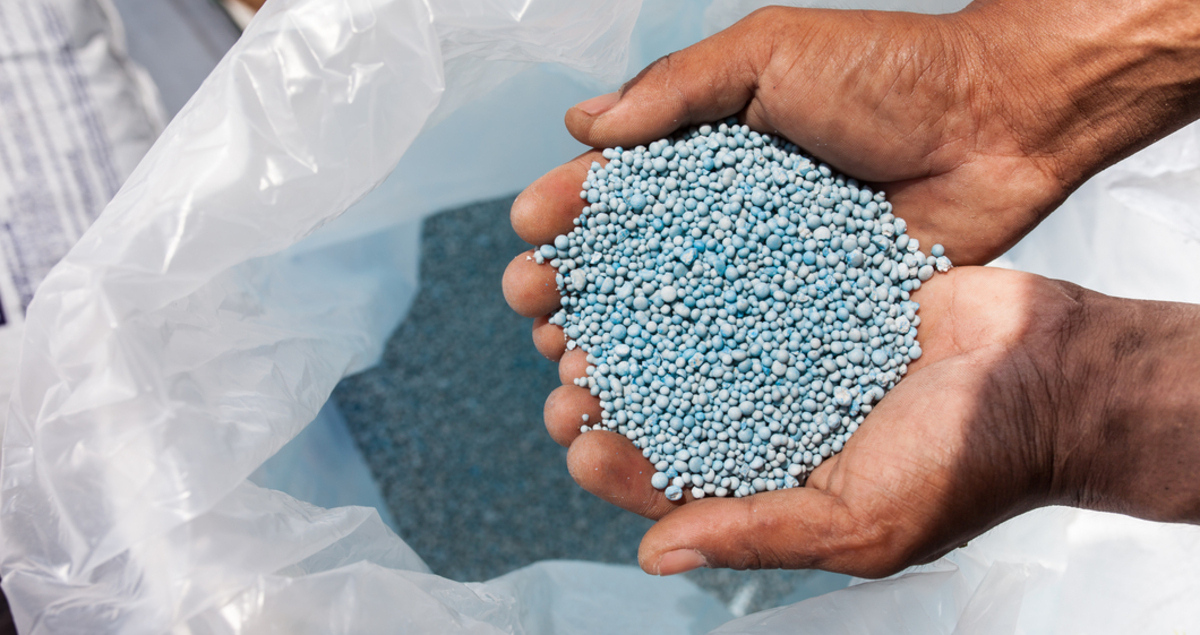
Taking the power sector to net zero
For now, the green hydrogen market remains nascent and doesn’t offer a solution to the immediate crisis. However, by reducing the dependency of industry and power generators on natural gas, hydrogen could improve energy security and help abate substantial quantities of CO2. Not only would such industry commitment set a more decisive course to net zero, but it would also boost green hydrogen’s growth, market maturity and scale.
And this is not a futuristic scenario: the power sector already has the option to convert existing natural gas-fired plants to ‘dual fuel’ operation. For example, Mitsubishi Heavy Industries (MHI) Group’s hydrogen-ready gas turbines can be fueled with either natural gas, hydrogen, or both.
MHI has so far shown that mixed combustion with a 30% share of hydrogen is possible, and is currently taking part in a project to convert three existing combined-cycle gas turbines (GTCC) from natural gas to 30% hydrogen mixed fueling at the Zero Carbon Humber cluster in the UK.
At the Intermountain Power Plant in Utah, United States, dual-fuel turbines will take over from coal in 2025. Initially, they will run on a mix of natural gas and 30% hydrogen and transition to 100% hydrogen by 2045.
Similarly, an existing co-generation system using a natural gas engine – which typically provides combined heat and power (CHP) in commercial settings – has successfully operated with a 35% hydrogen fuel mix.
This means the move to hydrogen becomes an upgrade rather than a ‘rip and replace’ undertaking, making the most of existing investments and infrastructure. Not only does this avoid the risk of being left with stranded assets, but it also reduces the cost involved in the transition to net zero emissions.

Decarbonizing steelmaking
In heavy industries such as steelmaking and cement production, it’s well known the biggest output isn’t steel or cement, it’s carbon. For every metric ton of steel, for example, 1.89 metric tons of CO2 are emitted.
The difficulty for steelmaking is that coal or natural gas are crucial as a feedstock for the underlying chemical processes and as a source of industrial heat.
Primary steelmaking based on natural gas (“direct reduction”) tends to be centred in regions with vast domestic resources such as Russia, the Middle East and the US, and gas supplies tend to be covered by long-term contracts.
However, electric arc furnaces – which are widely used in Europe – use electricity to melt scrap metal for steel production. This sector has been suffering indirectly from the gas crunch because it led to skyrocketing electricity prices.
Despite these differences, it is clear that steelmaking needs a greater variety of fuel sources.
Last year, hydrogen was used for the first time in commercial steel production to supply industrial heat at a plant in Sweden. And Primetals Technologies, an MHI Group company, has set up a pilot plant for hydrogen-based ironmaking in Austria.
But hydrogen alone is not a silver bullet, which is why the industry is also investing heavily in other technologies. These include the rollout of carbon-capture systems to filter out emissions and boosting scrap-metal smelting – with a view to using more renewable energy or converting waste heat from a plant’s operation into electricity.
Developing hydrogen-ready infrastructure
While governments around the world have committed heavily to bringing about the so-called ‘hydrogen society’, it’s important to acknowledge the market for hydrogen – as a ubiquitous, carbon-free fuel – is in its infancy. Several challenges need to be overcome.
Most hydrogen today is still produced from natural gas. This means it is affected by the kind of volatile market fluctuations we are currently seeing, and it also generates significant CO2 emissions of its own.
The International Energy Agency expects that, even in 2050, 50% of natural gas will still be used to produce hydrogen, albeit mostly in combination with carbon capture to reduce emissions (low-carbon, ‘blue’ hydrogen). It also says in its World Energy Outlook 2021 report that, while the technologies for generating low-carbon and entirely ‘green’ hydrogen from renewable sources are available, hydrogen projects are only slowly being rolled out commercially, and at scale. This applies to both the production of hydrogen and its distribution networks. The latter is critical because there is no comparable infrastructure for the distribution of hydrogen as there is for natural gas.
Both regulatory support such as the EU Commission’s Hydrogen Strategy and cross-industry, private-sector initiatives – like the Hamburg Hydrogen Network and H2@Scale in Texas – will be critical to connecting future producers and users of the gas.
Getting on the net zero pathway
Boosting hydrogen production and distribution will also be key to bringing the cost of green hydrogen down to viable levels for end users.
The gas crunch in Europe has meant that green, renewable hydrogen is now cheaper to produce than ‘grey’, natural gas-derived hydrogen, according to analysts ICIS. On a wider scale, however, the expectation is that green hydrogen will become cheaper than grey hydrogen by the end of the decade, without any carbon pricing. The Energy Transition Commission forecasts that the cost will drop below $2 per kilogram in most markets, or to even less where renewable energy is available more cheaply.
While this timeline may still look distant, one thing is clear: with less and less investment being put into fossil-fuel infrastructure, getting ready for the move to hydrogen is non-negotiable for industry. This will be essential, both to hedge against the next gas crunch and to get onto the pathway for a net zero future.
Discover more about MHI’s work on building the hydrogen value chain here
Related tags
