Green steel by 2030? Here’s what needs to happen next

“Green steel” that is made without using fossil fuels is already a reality. Ingots were handed out to delegates at the COP26 climate change talks in Glasgow as evidence of the proof of concept. The challenge ahead is to produce commercially viable emissions-free steel at scale to meet growing demand … and to do it quickly.
Steel was much discussed at the climate talks in Scotland. One of five key “Glasgow Breakthroughs” was the target for “efficient use and near-zero emission steel production, established and growing in every region by 2030”.
While the technology exists to create green steel — using hydrogen produced from renewable electricity — some challenges must still be overcome before this nascent process can be scaled up. And the main barrier is the vast amounts of green and blue hydrogen required.
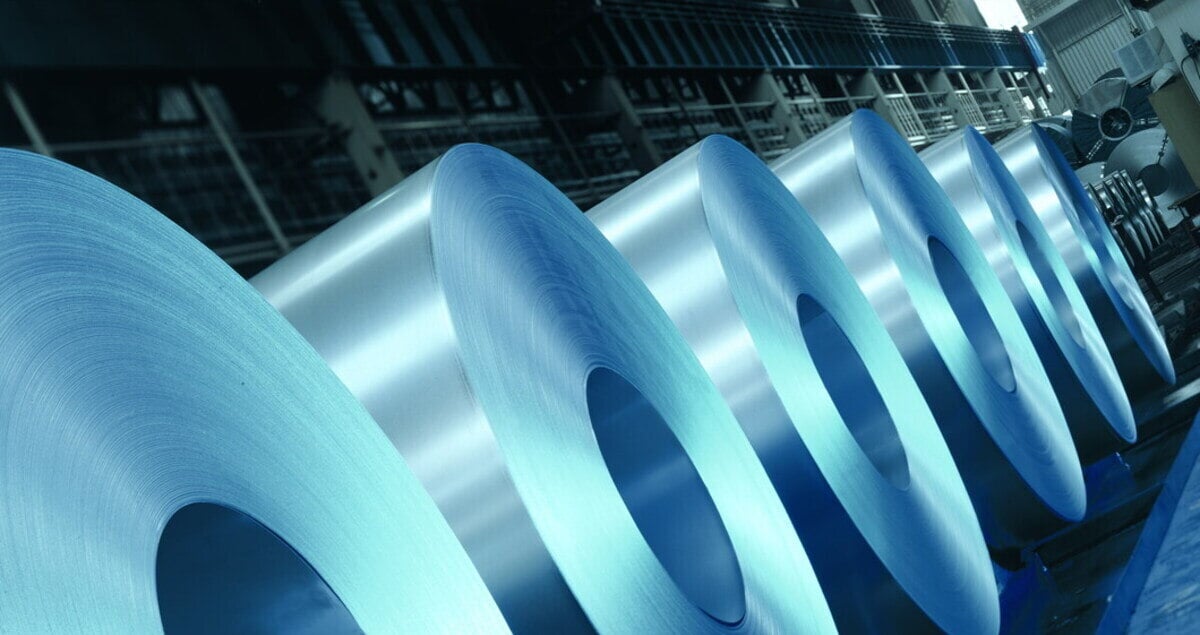
Hydrogen-based sustainable steel
Producing the steel we need for construction, machinery, transport and endless other applications depends largely on extracting iron — the base material of steel — from iron ores, which is an energy-intensive business.
Fossil fuel-powered plants are currently the only viable way to obtain high-quality iron at the scale needed to produce enough steel. This energy-intensive process means the industry actually produces more CO₂ than steel — around 2 tonnes of CO₂ are emitted for every tonne of liquid steel produced.
Steel emissions must be halved by 2050 and continue to decline thereafter to meet global energy and climate goals, according to the International Energy Agency’s “Iron and Steel Technology Roadmap”.
As steelmakers seek more sustainable production methods, hydrogen is emerging as a go-to solution that could drastically reduce the sector’s carbon footprint. When burned, hydrogen emits only water. And if that hydrogen is produced via electrolysis using just water and renewable electricity, then it is completely free of CO₂ emissions. Hydrogen can also be low carbon if produced with fossil fuels and carbon capture, utilization and storage technologies — so-called “blue hydrogen”.
Breakthrough technologies have been developed with the aim of eliminating emissions from steel production by using hydrogen instead of fossil fuels. One example is the HYFOR direct reduction pilot plant at a site of Austrian steel producer voestalpine, which was developed by Primetals Technologies, part of the Mitsubishi Heavy Industries (MHI) Group.
But to prove the business case for these technologies, they need to operate at scale to reduce costs, which would require a substantial increase in clean hydrogen production.
“The real roadblock for green steel is simply the availability of low-carbon hydrogen,” says Dr. Alexander Fleischanderl, Technology Officer, Upstream at Primetals Technologies. “Scaling up this technology will require massive amounts of green or blue hydrogen.”
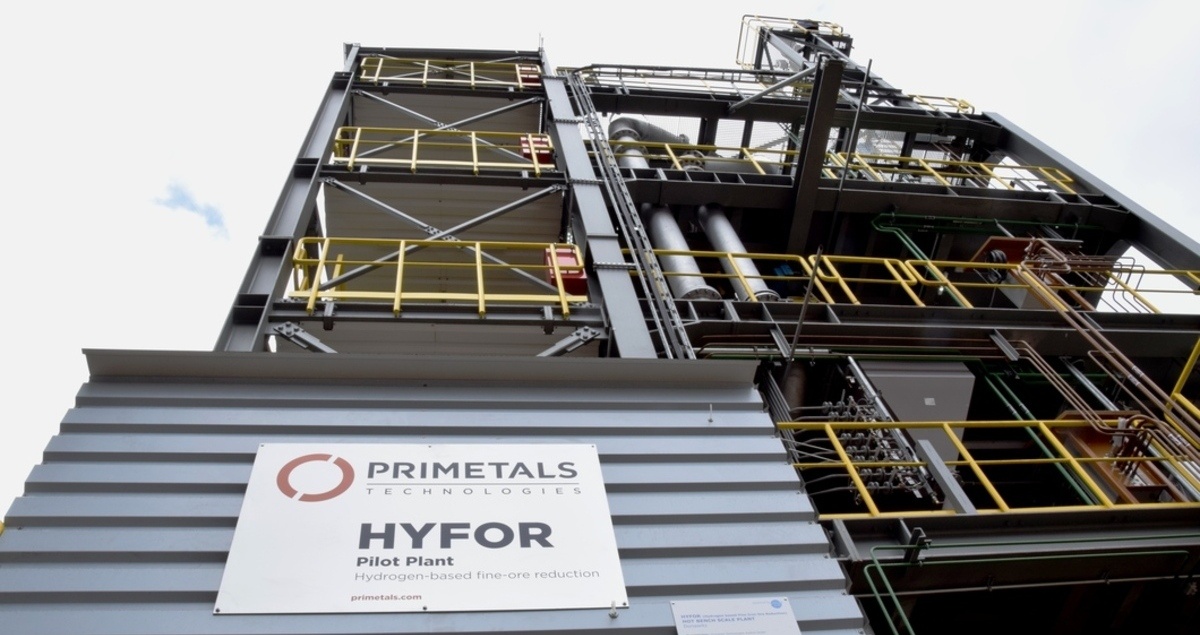
Kick-starting sustainable steel
So, what needs to happen to kick-start the green steel industry by the end of this decade?
It’s important to manage expectations, according to Dr. Fleischanderl.
“We are looking at realizing a small market share for emissions-free steel production by 2030, rather than transitioning fully,” he says.
Take-up of green steel will also vary between regions. Steelmakers in countries such as India and China, with heavy investments in new blast furnaces that have long life spans, will likely be slower to switch.
A green steel future rests on fine-tuning existing technology, scaling up production capacity and having abundant supplies of low-carbon hydrogen.
Policymakers can help build a framework that encourages the development of a clean hydrogen economy and allows sustainably produced steel to thrive, even with a premium price tag attached.
This includes three main pillars.
Establish a realistic carbon pricing system that makes hydrogen-based steel production more competitive.
Create a premium market for green steel to encourage companies, organizations and governments to make buying decisions based on sustainability, despite higher costs.
Provide sustainable funding instruments that drive low-carbon initiatives, such as those foreseen by the European Green Deal and tax incentives like the 45Q system in the US.
If policymakers can provide this support, then Dr. Fleischanderl is confident the market will do the rest.
“I think that any green steel that is produced will find its way into the market,” he says.
“There is currently more demand than there is green steel available, and customers are also willing to pay a certain premium [for it]. Clearly, end users want green steel, even if it costs more.”
Discover more about Primetals Technologies’ HYFOR hydrogen-based direct reduction technology
Related tags
