Getting more for less in modern manufacturing

Everyone always wants more for less: individuals, companies and governments. It’s the defining challenge facing businesses as they try to stay competitive. Manufacturing, in particular, has been through radical change as a result of globalization sharply increasing competition. But that doesn’t mean the sector can now stand still. Far from it. The challenges and the changes keep coming.
Smart factories
Increasing factory automation is an obvious way to reduce costs while maintaining quality. The Internet of Things, wearable technologies, robotics and Artificial Intelligence are just some of the technologies transforming traditional factories into ‘smart’ ones. This will ultimately enable companies to make the most of their resources and produce higher-quality goods more efficiently. A survey by Capgemini found that smart factories will enable a seven-fold increase in overall productivity by 2022, with capital and inventory costs expected to reduce 12-fold compared to 1990. The advent of smart factory technologies will also speed up production and help manufacturers respond more quickly to changing market needs. Typically, factories are set up for long, high-volume production runs. Today, it’s critical to be profitable at lower batch numbers and over much shorter product life cycles and have the ability to rapidly swap production to new products as needed. But Capgemini’s analysis shows that only 6% of manufacturers are ‘digital masters.’ Most of the businesses surveyed – more than 75% - fell into the ‘beginners’ category when it came to converting their production sites to smart factories. Clearly there is a lot more work to be done.
Shared goals
Mention the ‘sharing economy’, and most people will think of companies such as Airbnb and Uber. But the need to share resources rather than control the entire value chain is not a new concept. Mobile service providers have been sharing network infrastructure for several years, enabling them to extend their coverage at a reduced cost and risk. The ‘shared factory’ takes this idea one step further. Mazda and Toyota, are exploring the idea by building a joint factory in the US. Beyond sharing cost and risk, this move will give Mazda its first US factory, reducing exposure to tax and currency risks, while Toyota will be able to up production on some of its most popular vehicles. The companies have taken a stake in each other’s businesses to reinforce their partnership. In the light of the high capital costs associated with manufacturing, and the continued pressure the sector is under, this kind of collaboration is likely to become more common.
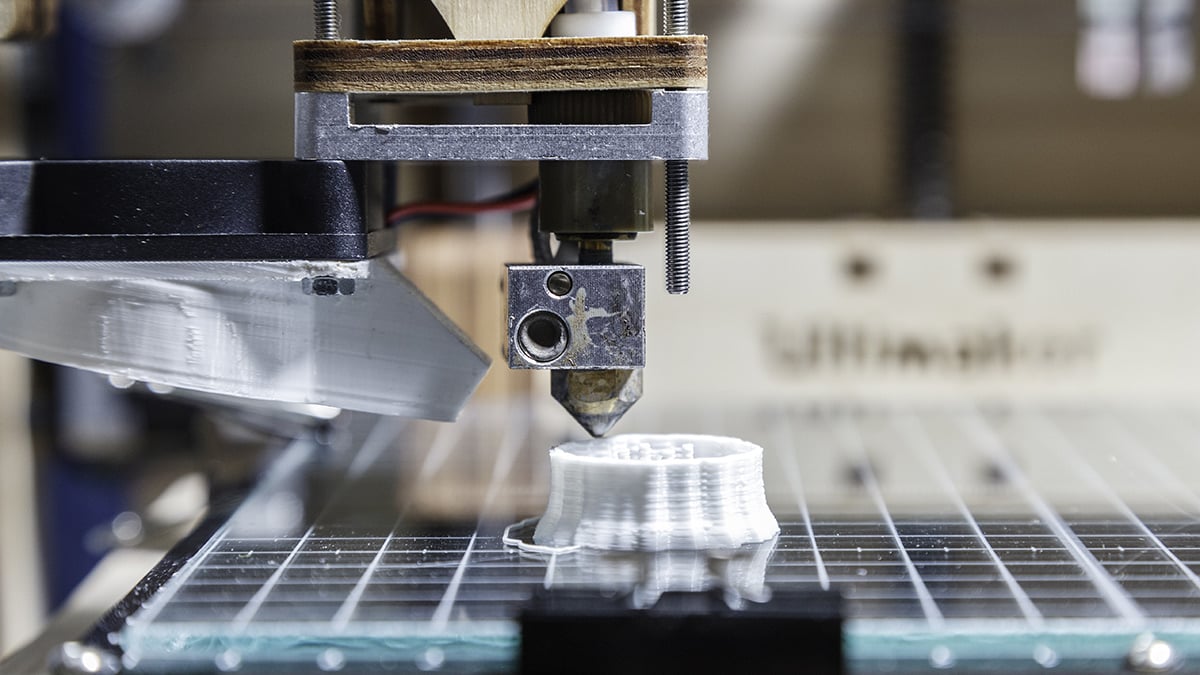
Innovating Step by Step
Collaboration is also at the heart of another trend in manufacturing: the use of incremental or ‘agile’ approaches to innovation. One of these is the Japanese business philosophy of ‘kaizen’, which favors step-by-step rather than abrupt, disruptive innovation. It encourages a culture where everyone is involved in jointly improving the organization by suggesting incremental changes to reduce costs, boost productivity or develop product features. This is diametrically opposed to the ‘big bang’ approach many companies have often resorted to, ring-fencing teams and resources for a set time to bring about one-off innovations. Instead, it is all about accumulating changes and adapting over time, with obvious practical and cost benefits over traditional innovation drives. Digitalization gives those practicing kaizen plenty of new opportunities. A wide range of data sources from across the organization can be mined to identify ‘gaps’ where improvements are needed.
Additive technologies come to the fore
Another game-changer in incremental innovation in manufacturing is 3D printing, or additive technology. With standard manufacturing techniques, it is expensive and time-consuming to produce prototypes of new products or parts. Using additive technology, it takes days rather than months to move a design from the drawing board to the real world, at a much-reduced cost. As 3D printing evolves, additive technology will also increasingly replace traditional production methods such as casting. Across the Mitsubishi Heavy Industries Group, for example, 3D printing is already used to produce components for turbines, turbochargers and aviation technologies, and has been critical in improving fuel efficiencies in these products.
A new generation of manufacturing workers
As these and other transformative technologies gain ground, the question is how they will affect the workforce. The World Economic Forum predicts a loss of five million jobs by 2020 due to automation and digitalization. At the same time experts agree that the need for highly skilled workers who can use new technologies will grow. Automation and digitalization promise an answer to many of manufacturing’s big questions, by helping the sector realize ‘more for less’. But this will only be possible if the industry can retain workers and enable them to switch to more skilled roles, overseeing the use of AI, robots and additive production methods. The challenge for manufacturing over the next decade will be to protect and grow technical skills, expertise and knowledge so it can continue to innovate and reinvent itself.
Related tags
