Boosting green hydrogen with solid oxide electrolysis cells

Hydrogen has been hailed as one of the key methods for decarbonizing industry and transport, with the number of new hydrogen initiatives increasing rapidly in recent years. Despite that, the International Energy Agency (IEA) says faster action is needed to reach net zero emissions by 2050 and meet the Paris Agreement’s targets.
While there is a broad range of CO2-free and low-carbon technologies to produce hydrogen, the main ‘clean’ production route is electrolysis. In this process, water molecules are split into hydrogen and oxygen using renewable sources such as solar and wind.
Bloomberg projects that the annual low-carbon hydrogen supply could grow 30-fold by 2030. While ‘blue hydrogen’ using traditional fossil-fuel synthesis and carbon capture will play an important role, the analysts expect more than half of this to come from electrolysis.

Among the technologies available, alkaline electrolysis currently accounts for the largest share of installed capacity at 60%, followed by proton exchange membrane (PEM) electrolyzers, which account for around 30% today, according to the IEA’s latest Global Hydrogen Review.
Recently, however, solid oxide electrolysis cells (SOECs) have been attracting growing attention as an additional path to generating carbon-free hydrogen. So, what are SOECs, and how can they help scale hydrogen production capacity?
What are the different types of electrolysis available today?
The most widespread production method, alkaline electrolysis, comprises two electrodes – an anode and a cathode – with a porous separator (diaphragm) between them. The most widely used electrolyte for hydrogen production is an alkaline solution of potassium hydroxide (KOH) in water. As electricity is applied to the electrodes, water molecules separate at the negatively charged cathode, releasing hydrogen. Alkaline electrolysis is known as a low-temperature technique and typically operates at 50-80°C.
While a mature technology with a long track record in areas such as sodium hydroxide production, alkaline electrolyzers can struggle with efficiency when synthesizing hydrogen as gas is not fully contained by the porous separator.
PEM uses a similar technological approach, at low temperatures, but with polymeric membranes as separators, which can better contain the gases that emerge from the reaction.
Finally, SOECs apply the same fundamental process but require much higher temperatures. SOEC systems typically need to be at temperatures of 800-1,000°C to function properly, though some start at 600°C. To cope with these high temperatures, they use ceramic cells as separators.
What are the advantages of SOECs?
As the reaction in the SOEC fuel cell progresses, electricity demand decreases, and some of the energy needed can be provided by the high operating temperatures. This means the technology can currently achieve efficiencies of up to 85%, according to Goldman Sachs Research; MHI’s SOEC development target is an efficiency of 90%. For alkaline and PEM electrolysis, electrical efficiency is around 70-75% at the top end.
“Because of this high efficiency, SOECs can theoretically produce more hydrogen per kW than any other type of electrolyzer,” Dr Kenichiro Kosaka explains. He is Chief Engineer and Senior Manager at Mitsubishi Heavy Industries’ Technology Strategy Department for Energy Systems and leads MHI’s electrolyzer development.
Historically, alkaline electrolyzers and PEM have been found to achieve longer life spans than SOECs. However, Kosaka points out that, theoretically, there is no big gap between SOECs and the other technologies, but a lot depends on the electrolyte material used.
Kosaka explains that the yttria-stabilized zirconia used in MHI’s SOECs has a lower conductivity than other electrolytes, such as gadolinium-doped ceria, but does not suffer the same level of degradation from the high temperatures at play.
MHI is developing SOEC technology at its Nagasaki Carbon Neutral Park and operating a test module at Takasago Hydrogen Park, the world's first integrated validation facility for technologies from hydrogen production to power generation. The company’s work on SOECs draws heavily on its experience with solid oxide fuel cells (SOFCs), which employ the same electrochemical processes, but in reverse.
How far along is the commercialization of SOECs?
In 2023, only about 1% of green hydrogen was synthesized by SOECs, the IEA says. However, commercialization is progressing, including rollouts of a green hydrogen facility at a refinery in the Netherlands and a system at a NASA research center in California.
MHI aims to bring to market large modular SOECs with an overall efficiency of 90%, designed for plants delivering several hundreds of megawatts by the end of the decade.
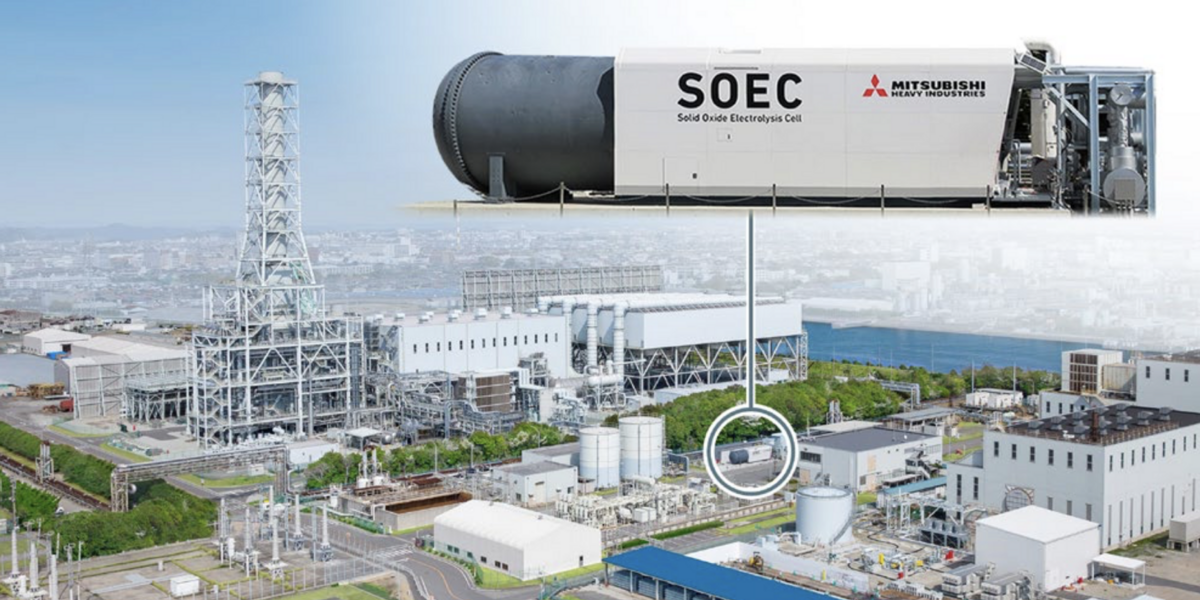
Access to rare elements is an important factor in the commercialization of electrolysis. Again, Kosaka points out, SOECs have an advantage. PEM relies on two precious metals, platinum and iridium, which count as some of the rarest in the world. SOECs do not require these, and the impact on demand for other rare metals – like nickel and zirconium – is projected to be marginal due to the higher efficiency of SOECs, Goldman Sachs Research suggests.
“On the whole, we believe SOECs are the most suitable technology for large-scale hydrogen production plants. While still emerging, what speaks for SOECs is their high efficiency and the fact that they derive from SOFCs, which can be considered a mature technology at this stage,” Kosaka says.
Broadening the electrolysis technology mix
There are also other electrolytic technologies at various stages of development, including anion exchange membrane (AEM) electrolyzers, the IEA says. With companies such as MHI and others involved in preparing AEM for commercial deployments, these are also likely to mature in the coming years.
However, green hydrogen production will not be a one-horse race, and the choice between different technologies will depend on the specific circumstances of each project.
For example, SOECs are particularly suited to large-scale applications with a stable power supply, Kosaka explains. This could be from non-intermittent sources such as geothermal, hydro, or nuclear energy, or a combination of those with renewables.
McKinsey predicts that clean hydrogen could account for as much as 73-100% of total hydrogen demand by 2050 if the most ambitious decarbonization scenarios are realized. To achieve this, CO2-intensive industries such as steel, cement and heavy transportation, as well as green energy producers, will need all the technologies they can lay their hands on.
The road to decarbonization is challenging, and while green hydrogen offers a viable route forward, it will need to be delivered at a much faster pace to fulfill sustainable energy commitments.
Discover more about MHI’s various hydrogen production technologies
Related tags
