Ammonia: Cracking hydrogen’s transport challenge

What do fertilizers, cleaning products and refrigerants have in common?
The answer is ammonia, a chemical compound composed of one nitrogen atom and three hydrogen atoms.
This composition has also brought ammonia to the energy industry’s attention. It offers a way for ammonia to solve the challenge of transporting hydrogen, an element increasingly seen as an alternative fuel to decarbonize large parts of the economy as it emits no CO₂ when combusted.
Transporting hydrogen is notoriously challenging, but using ammonia as a carrier enables safe shipping and storage of large volumes of hydrogen over long distances.
The key here is the “cracking” technology used to extract the hydrogen component once the ammonia reaches its destination.
Hydrogen’s transportation challenge
While natural geological sites like salt caverns can be used for local storage of hydrogen, the fuel’s potential starring role in the global energy transition depends on finding efficient ways to transport it — often over long distances — from production site to offtaker.
But this presents a challenge. Hydrogen is a gas at room temperature and has low volumetric energy density, so it can take up a lot of space compared to other fuels, making transportation inefficient.
Hydrogen can be compressed to boost its energy density, but very high pressures are needed to achieve relatively minor gains. And, while liquefying hydrogen more than doubles its density, this process is both inefficient and costly — liquefaction typically consumes almost a third of hydrogen’s energy content.
However, transporting hydrogen using a carrier such as ammonia or methanol — which have multiple hydrogen atoms — allows much greater volumes to be moved relative to the tank size.
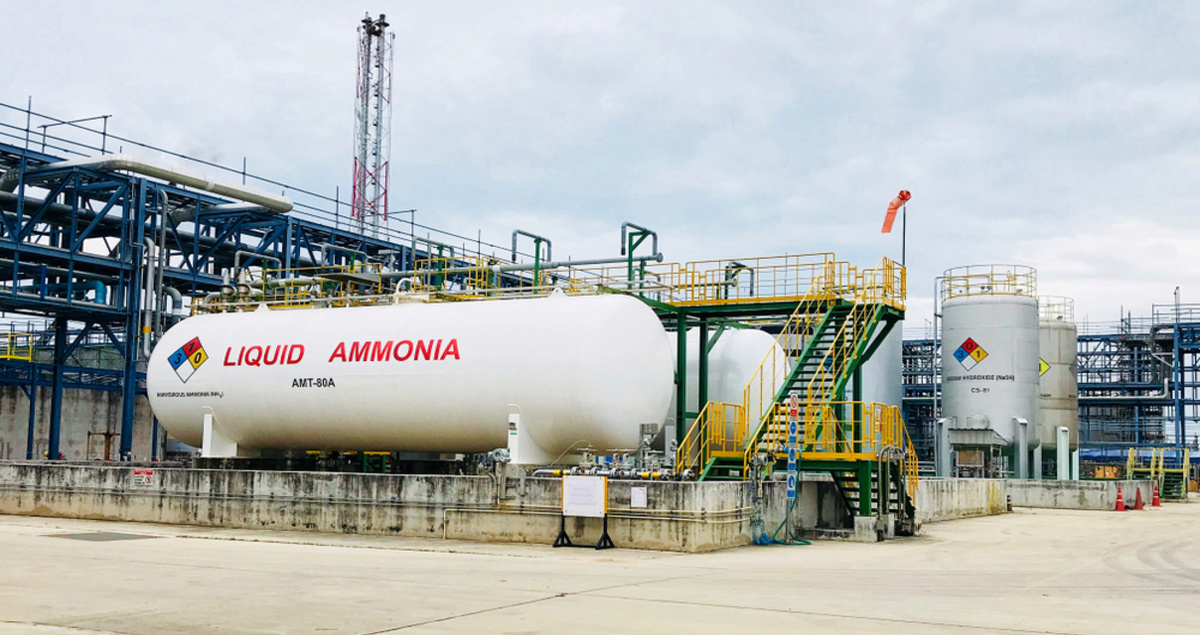
Safe, stable ammonia can overcome this problem
Ammonia is emerging ahead of methanol as the clear frontrunner for transporting hydrogen, because it has a much higher density as a carrier.
As a key component in fertilizer production, ammonia also has an established global supply chain with safe bulk shipping and storage standards. Tried-and-tested leak prevention practices are an advantage, given ammonia’s high toxicity, while its high ignition temperature makes ammonia safe to transport and store.
In its pure gas form, ammonia can be liquefied easily at room temperature using extremely low pressure, facilitating high-volume transport.
Upon arrival at its destination, the ammonia must undergo a “cracking” process to separate the hydrogen from the nitrogen.
Once the hydrogen is released from its ammonia carrier, the gas can be transported using existing natural gas pipelines adaptable to carrying hydrogen. It can then be used as a raw material in industrial processes or as an alternative fuel to help decarbonize heavy transport systems like trucks, trains, shipping or aviation.

A cracking solution
A recent study by the Port of Rotterdam found it is technically and economically feasible to safely convert ammonia into around 1 million tonnes of hydrogen annually at the port using a large-scale cracker.
As part of efforts to expand the use of hydrogen and ammonia, Mitsubishi Heavy Industries (MHI) Group is partnering with Nippon Shokubai to develop an optimal ammonia cracking system that could enable the use of hydrogen through the transportation of high volumes of ammonia.
Hydrogen from the new cracking system would be available for use as an emissions-free fuel and a raw material.
Cracking technology is a crucial part of efforts to establish a supply chain for using ammonia as a hydrogen carrier, and is gaining traction. Several pilot projects are underway in Europe and, in Japan, a joint study is being carried out to establish a hydrogen and ammonia supply chain in the Osaka coastal industrial zone.
Solutions like this could prove a valuable tool in establishing a global hydrogen network to help decarbonize supply chains.
Discover more about Mitsubishi Shipbuilding’s development for ammonia and liquefied CO₂ carrier
Related tags
